Creating back-contacted solar cells
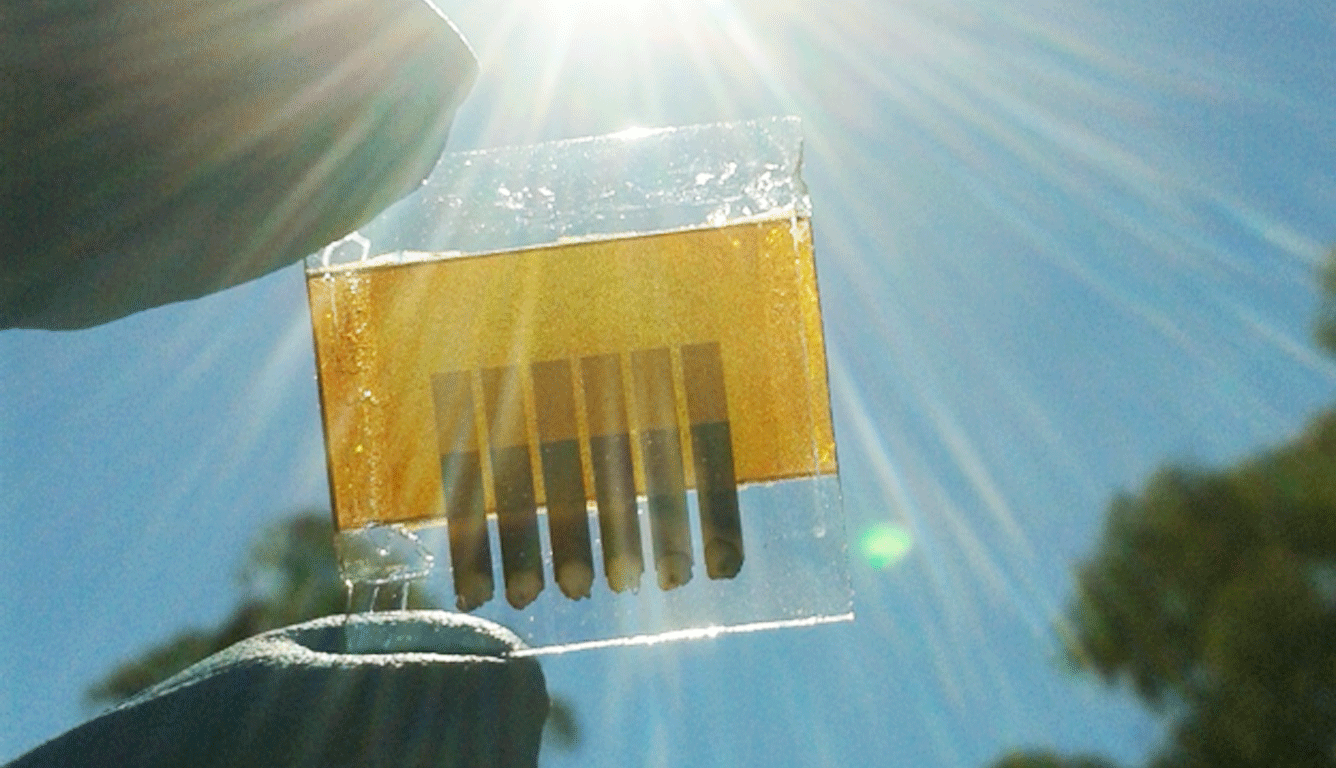
Researchers have found a way to manufacture back-contacted perovskite solar cells. Credit: Dr Askhat Jumabekov.
Solar cells are one of the most promising and accessible mechanisms by which the country can reduce its carbon footprint. However, the technology is still maturing and inefficiencies remain a barrier to widespread usage.
Now though, by combining the benefits of back-contacted solar cells with perovskite materials, researchers have achieved a much sought after pathway to more efficient photovoltaic devices.
Solar cells work by using a photovoltaic material to produce an electric current between an anode and cathode when illuminated by the sun. However, the way a cell is structured and the materials it’s built from can have a dramatic effect on its ultimate performance, and thus its relevance in real-world applications.
The two leading types of devices are currently back-contacted silicon cells and perovskite-based devices. They each have their own efficiency advantages, but also limitations.
Perovskite is a material which is incredibly good at taking in light and converting it to electrical energy. However, perovskite solar cells (PSCs) are currently built using a “sandwich structure”, which requires a conductive and opaque electrode above and below the photosensitive perovskite material, limiting the directions in which they can receive light, which reduces the overall device efficiency.
Back-contacted solar cells are the widely preferred method for collecting the electricity created by photovoltaic material. Building the electrodes into an underlying structure of the light-sensitive material reduces transmission losses associated with top-side electrodes and allows it to be illuminated from all sides. Back-contacted silicon photovoltaic cells have already been manufactured and are commercially available, but silicon isn’t as good as perovskite at converting light to electricity.
Adaptation of a back-contacted design to the perovskite solar cell is incredibly difficult as the interdigitated array of electrodes must be delicately structured, which provides a number of major fabrication challenges.
However, the latest research from a team of CSIRO and Monash University researchers, working out of ANFF-Vic’s Melbourne Centre for nanofabrication, has combined the benefits of both device types using a series of photolithography and vacuum deposition processes. The technique enabled an alternative design in which the interlocking array of anodes and cathodes were no longer on the same plane, but still remained on only one side of the perovskite absorber layer.
The result has, for the first time, demonstrated the possibility of constructing a back-contacted PSC. And while efficiencies are lower than what can currently be achieved in conventional silicon-based devices, the new cells have the potential to provide far higher conversion rates once optimised.
Now, the team are working to develop the processes used to make these cells in order to make them suitable for mass production. Once found, scalable, affordable fabrication techniques will bring back-contacted perovskite solar cells into the light, along with all the advantages they offer.
High performance microfluidics increase solar panel efficiency
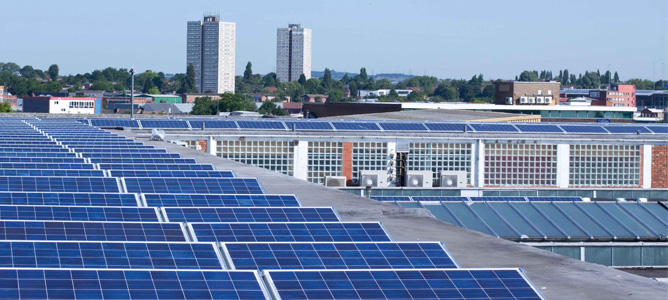
This project aims to increase the efficiency of standard solar panels which lose efficiency in high heat surroundings.
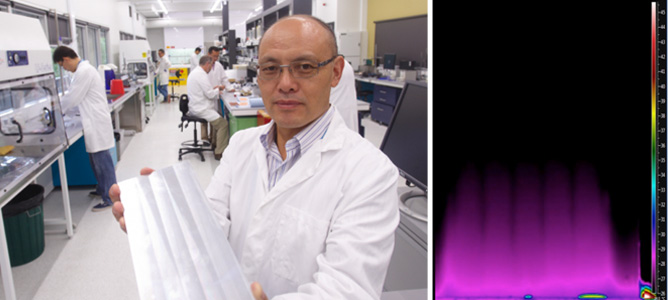
Left: A prototype heatpipe plate device developed at CSIRO held by Dr Yonggang Zhu; Right: the IR image of thermal conduction of the plate during start-up.
March 2015
The global drive towards making solar energy more competitive against low cost fossil fuels has given rise to some amazing solar technologies. However one of the biggest, but least publicised challenges that all solar cell researchers face is the stability and scalability of their inventions. For example, for every 10°C increase in operating temperature, most solar cells become around 5% less efficient in converting sunlight into electricity. Under the powerful Australian sun, this means a typical reduction of 10-15% of energy yield. It negates largely the efficiency improvement researchers have achieved over the last few decades for crystalline cells.
Since 2013, the CSIRO Microfluidics team led by Dr. Yonggang Zhu have been developing a novel thermal management system to address some of the fundamental challenges associated with solar photovoltaic- technologies. The project is part of a $4 million SIEF (Science and Industry Endowment Fund) project - ‘High performance solar cell technology with integrated nanoplasmonic thin film and thermal management systems.’ In this project, Swinburne University of Technology and CSIRO researchers are working jointly to overcome the efficiency losses that solar cells suffer when exposed to high temperatures.
In tackling this problem, the CSIRO team has developed a novel heatpipe plate system that can potentially be integrated with PV panels. The system utilises unique microscale thermal and fluids behaviors to remove heat with high efficiency. The devices were fabricated and tested in the Micro and Nanomanufacturing Laboratory, an ANFF Victoria Facility based in CSIRO Clayton site.
The heatpipe plate is fabricated of metallic materials and has a thickness of a few millimeters. It can be mass-produced to reduce costs. While there is internal microflow within the plate, the integrated device has no moving parts and can potentially last for over 10-20 years, making it ideal for integration with PV panels.
The technology developed from the project will generate benefits in energy sector by recovering the electricity loss due to heating effect by up to 10-15%. This will ultimately help reducing the green gas emission. In addition to energy, the technology can also be applied in a variety of other industries.The future work will focus on the integration of the system with PV panels and mass production techniques.
Better batteries possible with alternative electrodes
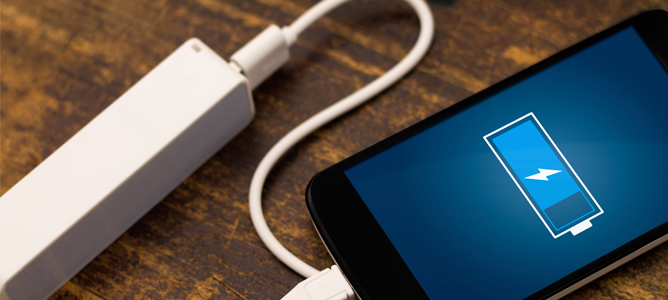
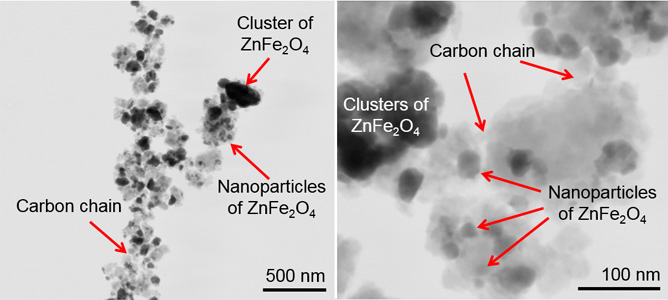
Low magnification (left) and high magnification (right) STEM images of ZnFe2O4-carbon nanocomposite electrode for Li-ion batteries.
April 2015
Lithium-ion batteries are currently used in every-day devices such as portable electronic devices and power tools. They are also of interest for other emerging applications including electric vehicle batteries and for storage of energy harvested by solar cells.
Graphite and lithium cobalt oxide are currently used in conventional lithium-ion batteries but these batteries may suffer from relatively small storage capacity. As a result, portable devices have limited time of use between recharges and the operation time of their battery decreases over the life of the battery. Similarly, electric vehicles are limited by the operation of their batteries and have limited driving range.
To improve the both the charge capacity and life span of these batteries, alternative materials for battery electrodes are currently being investigated by MCN Technology Fellow, Dr. Alexey Glushenkov from Deakin University. These new materials are expected to store more charge and remain active for longer periods of time. To select and optimise these materials, characterisation by electron microscopy is required to understand their structure and performance.
Through using the FIB-SEM at MCN which is fitted with Scanning Transmission Electron Microscopy (STEM) detectors, Dr. Glushenkov is able to select and study new electrode materials for Li-ion batteries. The electrode materials are synthesized by his team at Deakin University in joint effort with Dr. Md Mokhlesur Rahman. The unique capability of the FIB-SEM instrument available at MCN is its ability to perform scanning electron microscopy (SEM) and STEM on the same specimen simultaneously. This allows researchers to understand the morphology of materials, their structure and composition at the same time, without the need to use multiple instruments. In addition, the focused ion beam available on the instrument can precisely slice specimens when required.
The team has recently produced a novel nanocomposite material in which zinc iron oxide is mixed with carbon. Zinc iron oxide is seen as an interesting electrode material for batteries but it usually cannot deliver sufficient charge storage and its ability to operate in a battery deteriorates quickly. However, the composite of zinc iron oxide with carbon developed by researchers at Deakin can store a large amount of charge and retain its charge storage ability for an extended life-span. Through use of the FIB-SEM instrument at MCN, the team have established that the attractive charge storage ability was achieved due to a unique nanostructure of the composite which consists of chains of carbon material decorated with oxide nanoparticles (refer to STEM images above).
This project holds great potential for the development of better electrode materials for batteries and, as a result, more reliable, longer lasting and cheaper batteries with higher charge storage capacities. In turn, this benefits portable electronic devices, power tools, electric vehicles, integrated solar cell-battery packs and many other applications.
The team expects to apply the FIB–SEM instrument available at MCN to studying electrode materials not only for lithium-ion batteries but also for new, unconventional types of batteries. In particular, sodium-ion are currently emerging as a new type of batteries for many applications.
Artificial leaves enhance light-to-chemical energy conversion
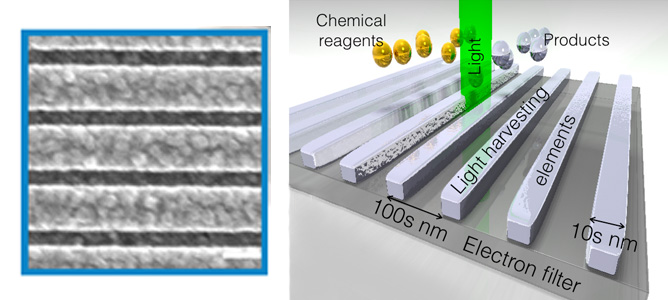
Left: SEM image of the top view of a fabricated artificial leaf (light harvesting structures), where the white bar corresponds to a length of 200 nm. Right: Diagram illustrating the artificial leaves and the size scales involved. Credit: D. Gomez
March 2015
Modern society is, to a very large extent, built on the products of the organic chemical industry. On a daily basis, these products are used for making pharmaceuticals, plastics, health and cosmetics products and for several items in the housing, transportation and telecommunication industries.
The chemical industry relies heavily on fossil fuel derived energy for carrying out these chemical processes. A more sustainable and desirable prospect is to harvest sunlight for doing chemistry and thus transform this industry into a solar chemical manufacturing industry.
This project aims to create novel ways to harvest solar energy for driving chemical reactions instead of generating electrical power. To this end, a team of researchers from CSIRO and the National Institute for Materials Scienc design in Japan, have fabricated nano-sized structures that are capable of harvesting light and converting it into chemical potential energy.
They have used the high-resolution electron beam lithography tool at MCN to create structures capable of efficiently harvesting light for driving chemical transformations, with some assessment of their performance carried out by collaborators in Japan.The artifical leaves, or light harvesting devices, are made out of a light harvesting component in direct contact with an electron filter. Each light harvesting element is made of Aluminium wires with a cross section of tens of nanometers. The spacing between the light harvesting elements is a critical parameter, with its magnitude is in the hundreds of nanometers which is controlled with a 10nm resolution.
Through this project they have demonstrated up to two orders of magnitude improvement in the rate of the chemical reaction of a test model using their light-harvesting system. They have achieved this by using a very simple configuration of nanostructures and anticipate that more spectacular light-to-chemical energy transformations can be achieved with more sophisticated nanoparticle deigns.
The team are currently creating more sophisticated nanoparticle systems that are capable of absorbing nearly 100% of the incident light across the visible spectrum. This will translate into much higher light-to-chemical energy transformation efficiencies and the team envisage that these light-harvesting technologies could be used for developing a sustainable and solar driven fine chemicals manufacturing industry in the not too distant future.
ALD could help prolongue battery life and improve reliability
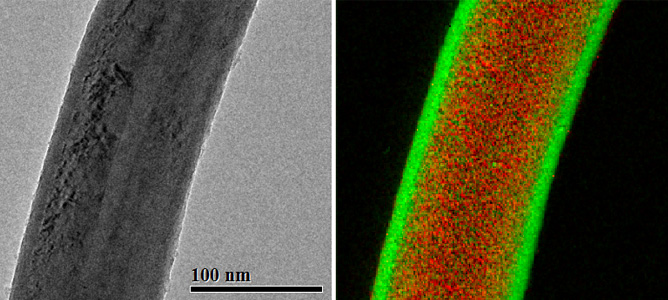
Left: A boron nitride nanotube coated with a 10 nm conformal layer of aluminium oxide (a bright-field TEM image); Right: energy-filtered image with elemental contrast (green – oxygen, red - boron).
November 2014
Improving the charge and life-span of batteries in phones, laptops and household technologies has the potential to improve not only efficiency and flexibility of these technologies, but also minimise the amount of toxic landfill created every year as a result of disused batteries.
MCN Technology Fellow, Dr. Alexey Glushenkov has been working on electrode materials for lithium ion and sodium ion batteries as well as electrochemical supercapacitors. A recent trial as part of this project saw a conformal deposition of 10nm of aluminium oxide onto boron nitride nanotubes by Atomic Layer Deposition (ALD). A normally challenging structure to coat uniformly, the nanotubes were coated by a homogeneous, 10nm thick layer of aluminium oxide using MCN’s ALD Savannah S100 instrument. The ALD techniques available at MCN are able to achieve highly conformal, continuous, pin-hole free depositions on complex surfaces and porous structures.
Dr. Glushenkov is aiming to use a similar technique to provide coatings for electrodes in batteries to provide an artificial surface layer to separate electrodes from direct contact with electrolytes in batteries. Such a surface layer is capable of ionic conduction and does not interfere with battery operation, while it works to reduce unwanted side effects caused by the contact of electrodes with electrolytes and result in better cyclic stability and reliability of batteries.
This project holds great potential for revolutionising the portable electronics industry and the way we interact with our devices.
Metal nanoparticles lead the way towards solar water decontamination
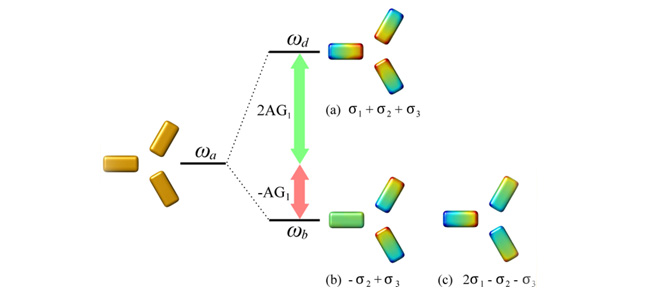
Three lowest-order modes of an interacting triangle of particles. Mode a) is the highest in energy of the three and is a mode with radial symmetry. Modes b) and c) are degenerate modes which are characterised by having a net dipole moment and perpendicular polarisations.
April 2014
It has long been known that solar energy can be used to create electric energy for heating and lighting. It can also be used however, to drive important chemical transformations such as the production of renewable chemical fuels by extracting hydrogen from water and hydrocarbons from carbon dioxide. Other uses include the sequestration of air pollutants such as greenhouse gases, low-cost water purification for developing countries, and the low carbon-footprint production of fine chemicals such as disinfectants and self–cleaning surfaces. There are countless other as yet unforeseen applications of solar to chemical energy transformations.
Existing approaches for harnessing solar energy for these applications are relatively inefficient and therefore not widespread. In order to improve the efficiency of solar-to-chemical energy conversion processes, it is important to maximise the light collection efficiency.
In this project, researchers from CSIRO led by MCN Technology Fellow Dr. Daniel Gomez, are creating novel metal nanoparticles capable of efficient light collection and focusing, in order to enhance the efficiency of light-driven chemical reactions. Utilising the Electron Beam Lithography (EBL) system, thin film deposition and characterisation tools available at MCN, the team have created networks of precisely controlled metal nanoparticles with precision down to 10nm.
Preliminary results indicate that certain nanoparticle arrangements can lead to an enhancement of light-driven decomposition of water pollutants by at least eight times the current rate of decomposition. They have achieved this by creating arrays of nanoparticles using aluminium, an abundant and inexpensive metal, which offers great potential for future deployment in large-scale applications.
The team are currently optimising the shapes and geometrical arrangements of the nanoparticles to achieve optimal rates of photochemical rates. Through this optimisation process they are addressing key fundamental questions, which will provide guidance in the development of processes for creating complex hydrocarbons from carbon dioxide.
You can read more about this project in The Dark Side of Plasmonics, published in Nano Letters.
Microflow batteries the future for electric cars
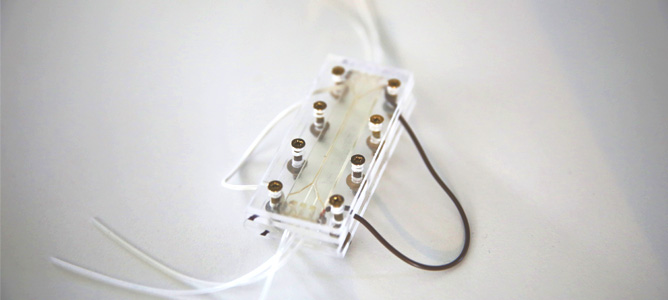
A micro-flow battery developed by Eden Research and Development
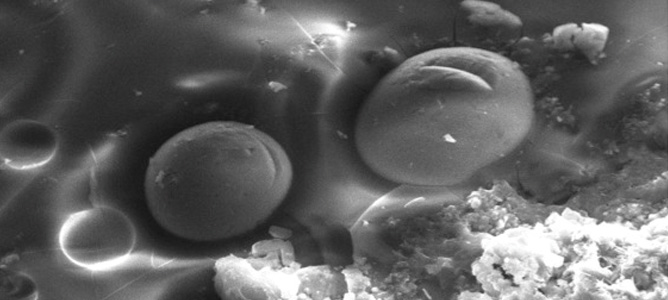
An Edenglass nanoparticle emerging from metallic oxide glass
July 2013
Eden Research and Development, an unlisted public company, has taken residency at MCN to develop a number of energy-related inventions. The first device built at MCN is a micro-battery using self-assembling nanocapacitors derived from proprietary metallic oxide glass with potential application as an electric car battery (or other energy storage applications) due to its size, safety and low cost profile.
The Eden micro-battery is believed to be the world’s first microfluidics battery using a miniaturised electrolyte (vanadium) flow battery design. In a flow battery, the electrolytes are charged and discharged in a cycle that is repeated thousands of times. The benefit of flow batteries is that they can be discharged down to zero charge at every cycle without suffering damage.
The overall construction of the chip was made on the MCN Eden 260 3D printer using a special transparent epoxy acrylate resin. The micro-battery uses a third electrolyte stream containing nanocapacitors instead of an ion permeable membrane that is normally used in vanadium flow batteries, which results in a substantial increase in both power and energy density.
An advantage of this micro-flow battery in an electric car will be that it can be recharged from the recovered energy of the moving car, minimising the recharge time required for the vehicle. The method used to collect and store this energy comes from a vitreous catalyst constructed from nanoparticles. These particles are nano sized capacitors, which are understood to attract charged ions, store them in its surface skin and be available on demand. The flow of ions in the cycles triggers the nano capacitors to release the ions and contribute to the current.
Eden’s Technical Director, Dr. Ross Mack said “We are very grateful to MCN for their assistance to date. The tools and instruments available at MCN are excellent, the staff are highly qualified and the Victorian Government is to be congratulated for having the vision to create the centre.”
For more information, visit www.edenbdm.com
NB: The material for this case study has been provided by Eden Research and Development. Although care has been taken to ensure the accuracy and completeness of the information that is provided, the MCN assumes no responsibility in relation to the interpretation or use of this information.
Harvesting sunlight to fuel the modern world
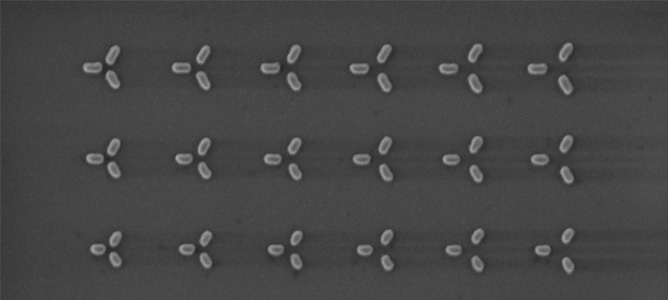
A Scanning Electron Microscope (SEM) image of a set of nanoparticles designed for capturing light. The basic design consists of an isosceles triangle of nanorods. Each nanorod is made of gold. By changing the sizes and separation among the nanorods, we can control which part of the solar spectrum get trapped by the nanoparticle trimer.
March 2013
Harvesting energy from light sources, including the sun, could provide a significant percentage of the world’s energy needs over the next century. In order to meet this critical demand, it is crucial to devise ways to transform light energy into chemical fuels, not just electricity. The aim of this project is to create new nanostructures that directly couple light energy into chemical reactions. In this study, researchers from CSIRO and the University of Melbourne, led by MCN Technolgy Fellow Dr. Daniel Gomez, performed the first step in this process - capturing and storing light energy with a system of nanoparticles.
The team created a system of nanoparticles that captures a significant amount of light which is able to store this energy for longer than most traditional systems. This feat is achieved by suppressing “re-radiation of light” by using metal nanoparticles that do not efficiently radiate light. The basic design consists of three metallic nanorods arranged in the shape of an isosceles triangle.
The metal nanoparticles were firstly designed at the CSIRO and The University of Melbourne using a sophisticated but simple theoretical model. The design was later transformed into real nanoparticles at MCN and was later put into action by testing their optical properties at the Optics laboratories at the University of Melbourne.
The nanoparticles were created using the electron beam lithography tool in the MCN cleanroom in addition to high resolution imaging equipment (scanning electron microscope), optical characterisation equipment (spectroscopic ellipsometer) and advanced metal processing tools (electron beam evaporator).
The most significant aspect of this project is that the team have achieved light trapping at the nanoscale by design. Starting with a highly sophisticated theoretical model of nanoparticles, they were able to create a structure that was able to interact with light (of particular wavelength and polarisation) and trap it more efficiently than most common systems. No single publication to date comprises a set of experimental and theoretical results as consistent and homogenous as the one presented by the group on the subject of ‘dark plasmonic modes.’ Due to the experimental precision, the excellent qualitative agreement between experimental data and the theoretical model and the large parameter space investigated, their study is a strong first step in the greater goal of creating solar fuels.
This study leads the way in a succession required for demonstrating solar-to-chemical energy conversion. While the general public often associates solar energy to the generation of electricity, sunlight can also be used for driving important chemical reactions such as the production of solar fuels. Some of these fuels include hydrogen gas, whose only product after combustion is water (not even a small trace of CO2, thus a fully carbon emission free technology). The outcomes of this grand challenge, namely using nanotechnology for solar-to-chemical energy conversion, will lead to low emissions, renewable energy sources and to a future Australian nanomaterial manufacturing industry.
After capturing light, the next step is to devise ways to do useful work with the energy trapped from it. The team at MCN will incorporate the nanoparticle designs into advanced architectures to demonstrate key chemical reactions driven entirely by sunlight.
Self-assembling gold nanorods show huge potential
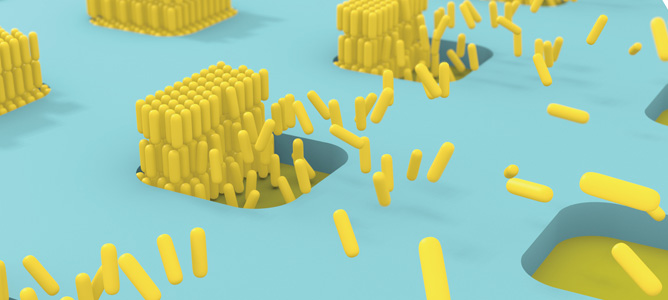
Illustration of the self-assembling of gold nanorod verticle arrays on patterned substrates.
July 2013
Nanostructures fabricated with metal nanoparticles hold great potential for applications in biosensing, optical analysis, computing and solar energy conversion. One approach to creating nanoparticle-based nanostructures is to program the spontaneous self-assembly of nanoparticles into the desired architecture.
Advanced self-assembled structures can be achieved with anisotropic nanoparticles like gold nanorods. This challenging self-assembly requires not only the control over the nanoparticles position but also their orientation at the nanoscale. MCN Technology Fellow, Associate Professor Udo Bach and his team have developed a self-assembly strategy to fabricate vertical arrays of gold nanorods on patterned substrates. This illustrates the possibility to program the self-assembly of anisotropic gold nanoparticles into complex structures with a precise orientation and placement on surfaces.
The gold nanorods were synthesised based on a well-known chemical protocol while the patterned substrates fabricated through cleanroom lithographic processes. The surface treatment and geometry of the patterned substrate are designed to guide the self-assembly of gold nanorods into vertical arrays.
The experiment consists of immersing a patterned substrate into a solution of gold nanorods and letting it dry with a controlled concentration and temperature. During the solvent evaporation, the nanoparticles spontaneously self-assemble onto predefined areas into vertical arrays over the entire substrate.
The nanostructures were then characterised by Small Angle X-ray Scattering (SAXS) in collaboration with the Australian Synchrotron. The help of Dr. Stephen Mudie allowed the team to gather important information about the self-assembly method such as the nature and the range of nanoparticle ordering, and the average interparticle distance.
The most exciting breakthrough was the ability to self-assemble these vertical arrays of gold nanorods with an unprecedented control over their placement on a surface. These results show an approach to address the issue of advanced nanostructure integration in functional devices, reducing the gap between nanomaterials and nanotechnology.
The group have demonstrated that the nanostructures can be used as a chemical sensor. It was up to 36 times more sensitive than a commercial substrate. One of the first benefits would be to design and optimise these nanostructures to fabricate ultrasensative sensors for chemical and biological molecules.
Beside the development of ultrasensitive biosensors, vertical arrays of gold nanorods could be used in optics. They can guide the light at the nanoscale in a structure called a waveguide. These gold nanorod arrays have been shown in the literature to be excellent waveguides. The idea would be to make an ideal substrate to self-assemble these gold nanorod arrays and to test their optical properties as waveguides.
You can read more about this project in Self-Assembly of Vertically Aligned Gold Nanorod Arrays on Patterned Substrates, published in Angewandte Chemie.
Vertical arrays of gold nanorods achieved
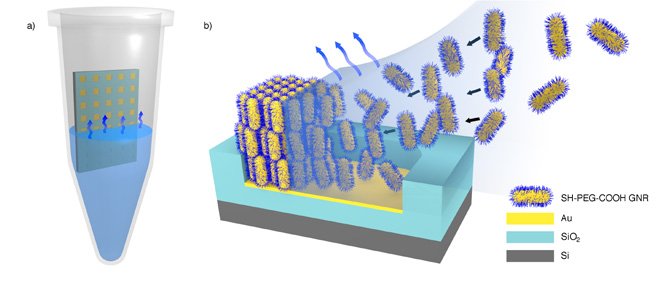
(a) Illustration of the experimental setup. The micropatterned substrate is placed in the centre of an Eppendorf tube and immersed in a concentrated colloidal solution of GNR’s. The substrate is left to dry under isothermal conditions. b) Schematic representation of the formation of standing arrays of GNR’s on a template upon solvent evaporation.
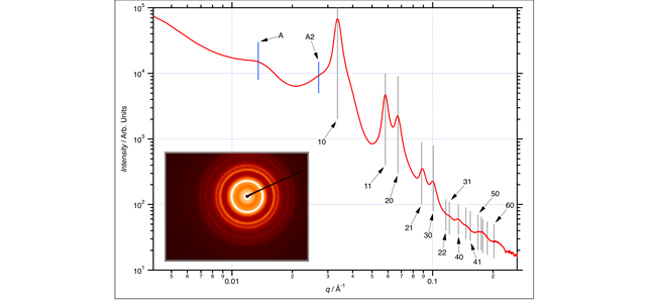
Transmission SAXS pattern recorded on a 100 μm × 250 μm section. Gray lines indicate the positions of the hcp reflections (labels are Miller indices (hk) for the reflections; not all are shown for clarity). The inset shows the associated diffraction pattern.
October 2011
Fabrication of novel self-assembly metallic nanostructures shows great potential for applications in biosensing, optical analysis, computing and solar energy conversion.
Working collaboratively with Instrument Manager Matteo Altissimo, Thibaut Thai of Monash University has combined bottom-up self-assembly processes with top-down techniques to generate vertical arrays of gold nanorods on patterned substrates.
Gold nanorods (GNRs) are of particular interest to researchers as they display unique yet highly variable optical properties. One such property is their remarkable sensing ability, which is exploited during Surface Enhancement Raman Spectroscopy (SERS). During this process GNR’s are closely packed together in a hexaganol-type arrangement forming high density “hot- spots”. If a molecule is within this “hot-spot”, its Raman signal will be greatly amplified.
The Raman signal then acts as a molecular fingerprint and is key in characterising a materials’ chemical structure, temperature or frequency mode.
In past research, controlling the self-assembly process has been a challenge due to the anisotropic nature of the nanorods.
Using a method developed at MCN, researchers were able to control the orientation of the assembly and select a precise location to express the desired features. The mask aligner, reactive ion etching process, electron-beam evaporator and scanning electron microscope were all critical components during the fabrication process.
The accuracy of the micro-patterns was confirmed using small-angle X-ray scattering (SAXS), a characterisation process undertaken using the SAXS beamline at the Australian Synchrotron National Research Facility.
In addition to showcasing the vast array of fabrication and characterisation tools available within MCN, the work highlights the unique relationship between the Australian Synchrotron and MCN, acting in unison as a hub for world-class research.